Iot Global IoT Remote Monitoring: Applications and Functions
Iot Global IoT Remote Monitoring: Applications and Functions
Blog Article
Remote Iot Monitoring Solution Custom Solutions for Asset Monitoring
The landscape of manufacturing is evolving rapidly, driven primarily by technological developments. Among these advancements, IoT connectivity solutions for manufacturing automation stand out as pivotal components reshaping how industries function. The Internet of Things (IoT) integrates digital and bodily worlds, creating a network of interconnected units that communicate seamlessly. This interconnectedness permits producers to optimize their processes and improve productiveness.
Real-time data is a cornerstone of modern manufacturing. Through IoT connectivity solutions, machines and sensors generate data that present insights into production processes. This immediate access to information empowers manufacturers to make knowledgeable decisions shortly. For occasion, if a machine is underperforming, operators can determine the difficulty and implement corrective actions directly, finally minimizing downtime and enhancing throughput.
Iot Global Asset Management with IoT Monitoring
Predictive maintenance is another vital advantage of IoT connectivity solutions. By constantly monitoring tools efficiency via quite a few sensors, manufacturers can anticipate failures before they occur. This proactive strategy drastically reduces maintenance costs and improves the lifecycle of machinery. Instead of adhering to a reactive maintenance technique, organizations can optimize their maintenance schedules primarily based on actual machine situations.
IoT expertise additionally facilitates better supply chain management. With the mixing of sensors throughout the provision chain, producers acquire enhanced visibility into stock ranges and materials flows. This improved visibility permits companies to optimize inventory administration, making certain that they've the required materials available without overstocking. Such efficiency translates to reduced costs and improved service levels, which are essential for sustaining a aggressive edge.
Iot Revolution Technologies Stand-Alone Remote Monitoring Devices
Automation and robotics are more and more reliant on IoT connectivity options. Smart factories combine automated systems powered by IoT to streamline production processes. Robotics geared up with IoT capabilities can communicate with each other and regulate their actions based mostly on real-time knowledge from the environment. This degree of synchronization permits the implementation of adaptive manufacturing methods that reply to fluctuations in demand rapidly and effectively.
Implementing IoT connectivity options requires a solid network infrastructure. Manufacturers must put money into reliable and secure communication networks able to handling the immense knowledge generated by interconnected units. 5G know-how is rising as an important enabler of IoT connectivity in manufacturing. Its speedy pace and low latency assist the real-time functions which might be important for data-driven decision-making.
Iot Remote Monitoring Solution Remote Insights through IoT Monitoring
Data analytics plays an important function in harnessing the full potential of IoT connectivity solutions. With a wealth of knowledge generated from connected units, producers must employ superior analytics tools to extract actionable insights. Machine studying algorithms can establish patterns and anomalies in data that will not be obvious to human analysts. This data-driven approach enhances operational efficiency by driving continuous improvement throughout manufacturing processes.
Cybersecurity is a vital consideration as producers combine IoT options into their operations. The connectivity that IoT brings increases the floor area for potential cyberattacks. Implementing strong security measures to safeguard critical manufacturing methods is paramount. This includes ensuring that each one gadgets are secure, data is encrypted, and steady monitoring for threats is in place.
Iot Remote Monitoring Solution Top 10 Monitoring Tools for IoT
Worker security is significantly improved via IoT connectivity options. Wearable units equipped with sensors can monitor the health and safety of employees in actual time. These smart wearables can alert personnel to hazardous situations, ensuring timely intervention. Such measures not solely shield workers but additionally contribute to general productivity by minimizing the risk of accidents.

The transition to smart manufacturing by way of IoT connectivity options additionally promotes sustainability. By optimizing processes, producers can considerably scale back waste and energy consumption. IoT units help track resource utilization, enabling companies to establish areas where efficiency can be enhanced. These environmentally friendly practices not only profit the planet but can even result in value financial he said savings over time.
The impact of IoT connectivity options on manufacturing extends beyond the operational realm. They enable enhanced customer engagement by permitting manufacturers to deliver customized products and services. Through IoT-enabled gadgets, manufacturers can gather data about customer preferences, resulting in the creation of tailored choices that better meet market calls for. This stage of engagement fosters customer loyalty and strengthens model reputation.
Iot Remote Asset Monitoring Solution Enhancing Efficiency with IoT Monitoring
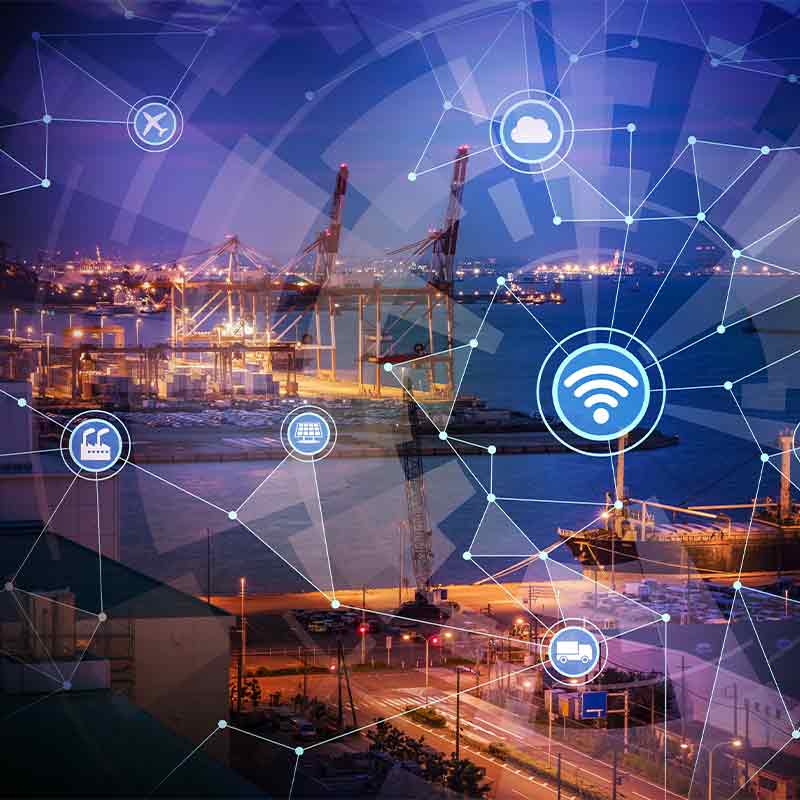
In conclusion, IoT connectivity solutions for manufacturing automation represent a transformative pressure within the trade. By offering real-time insights, predicting tools failures, bettering supply chain management, and enhancing worker safety, these solutions redefine operational effectivity. As manufacturers proceed to combine IoT technologies, the benefits prolong beyond conventional metrics of productivity and price. Embracing these improvements sets the groundwork for a extra sustainable and responsive manufacturing environment that is outfitted to satisfy the challenges of the longer term.
- Enhanced real-time monitoring through IoT sensors permits manufacturers to track machinery efficiency and operational efficiency.
- Predictive maintenance is facilitated by IoT connectivity, lowering downtime and lengthening tools lifespan via timely interventions.
- Seamless integration of IoT units across production lines enhances knowledge collection, resulting in improved decision-making processes.
- Wireless technologies corresponding to LPWAN allow cost-effective communication over vast manufacturing facilities, minimizing installation complexity.
- Cloud-based IoT platforms provide scalable solutions for information analytics and visualization, empowering manufacturers to determine tendencies and optimize workflows.
- Enhanced asset tracking using IoT gadgets ensures better stock administration and lowered losses because of misplacement or theft.
- Industry-specific IoT protocols, like MQTT and CoAP, guarantee environment friendly and safe data transmission tailored to manufacturing wants.
- Advanced cybersecurity measures are essential in IoT ecosystems to protect sensitive operational information from potential threats and breaches.
- Integration of IoT with machine learning algorithms permits for autonomous changes and improvements in production processes based on historic data.
- Collaboration with IoT resolution suppliers enables producers to customise connectivity methods that tackle their unique operational challenges.
What are IoT connectivity solutions for manufacturing automation?
IoT connectivity options allow seamless communication between machines, sensors, and units inside a manufacturing environment, facilitating data exchange, monitoring, and control to reinforce operational efficiency and decision-making.
How do IoT connectivity solutions improve manufacturing processes?
Remote Monitoring Understanding Remote IoT Monitoring Benefits
These options streamline workflows, cut back downtime, and optimize asset utilization by offering real-time information insights, enabling predictive maintenance, and enhancing supply chain visibility.
What forms of IoT connectivity technologies are generally used in manufacturing?
Common technologies include Wi-Fi, Zigbee, LoRaWAN, cellular (4G/5G), and Bluetooth. Each technology presents distinctive advantages based mostly on range, information switch pace, and energy consumption fitted to totally different manufacturing needs.
Remote Iot Monitoring Solution Top 10 Monitoring Tools for IoT
How secure are IoT connectivity solutions for manufacturing?
Robust safety measures, including encryption, system authentication, and community segmentation, are important to guard manufacturing environments from cyber threats, making certain knowledge integrity and operational continuity.
Can IoT connectivity options be built-in with current manufacturing systems?
- Remote Monitoring
Yes, many IoT solutions are designed for interoperability, allowing integration with legacy methods and gear. This enables manufacturers to boost their capabilities without changing present infrastructure.
It Remote Monitoring Software Basics of IoT Remote Monitoring

What are the cost implications of implementing IoT connectivity solutions?
Initial setup prices might vary, however long-term financial savings are often realized through elevated effectivity, reduced waste, and improved maintenance methods. A detailed cost-benefit evaluation might help decide the monetary impact. Remote Visit This Link Monitoring Solutions.
How can I choose the best IoT connectivity solution for my manufacturing facility?
Evaluate elements such as scalability, reliability, ease of integration, and specific use case necessities. Consulting with business consultants and conducting pilot tasks may help in identifying the most effective fit on your wants.
Remote Iot Monitoring Solution Condition Monitoring with IoT Alerts
What are the challenges in adopting IoT connectivity solutions for manufacturing?
Challenges might include cybersecurity issues, interoperability issues, and the need for staff coaching. Addressing these obstacles through strategic planning and stakeholder involvement can facilitate profitable adoption.
How does data collected through IoT connectivity affect decision-making in manufacturing?
Real-time information analytics permits manufacturers to make informed selections quickly, optimizing operational processes, improving high quality control, and enabling proactive administration of resources and potential points.
Report this page